Introduction
In the pharmaceutical industry, quality and compliance aren’t just buzzwords—they’re essential. The FDA’s Current Good Manufacturing Practices (cGMP) ensure that medicines are consistently produced to meet stringent safety, quality, and efficacy standards. But while much of the focus is on processes and materials, one critical component often overlooked is the role of insulation.
What is cGMP?
cGMP refers to the FDA’s formal regulations governing the design, monitoring, and control of pharmaceutical manufacturing processes and facilities. These guidelines ensure that products are:
- Produced with consistent quality.
- Free from contamination.
- Manufactured using materials and methods that meet stringent safety standards.
To achieve cGMP compliance, manufacturers must establish robust quality management systems, utilise high-quality materials, and adhere to standard operating procedures (SOPs). The FDA conducts regular inspections to enforce these practices, with non-compliance leading to serious consequences, including product recalls or facility shutdowns.
Why Insulation Matters for cGMP Compliance
While insulation may not seem directly related to cGMP, it plays a crucial role in maintaining a compliant manufacturing environment:
- Moisture Resistance: Insulation that allows moisture penetration can lead to corrosion under insulation (CUI) and bacterial growth, threatening product safety and cleanroom sterility. T-FIT Clean insulation prevents these risks with its closed-cell foam structure and high-water vapour diffusion resistance.
- Fungal Resistance: Mould and fungi can contaminate products and environments, risking non-compliance. T-FIT insulation is made from foam that does not support mould growth as shown by the zero-mould growth rating achieved against ASTM G21.
- Low Outgassing: Materials used in cleanrooms must have minimal emissions of volatile organic compounds (VOCs) to maintain air quality.
- Leading Fire Safety Credentials: The only foam compliant with the FM4910 Global Cleanroom Materials Protocol, it also achieves a UL certified rating of 0/10 for surface burning characteristics when tested to UL 723 (also known as ASTM E84)
T-FIT Insulation: A Partner for Compliance
T-FIT Clean insulation has been a trusted choice in pharmaceutical facilities worldwide. Its unique properties align seamlessly with cGMP requirements:
- Barrier to Contaminants: The smooth, non-porous surface prevents debris and microbial buildup.
- Proven Track Record: Facilities using T-FIT Clean consistently pass cGMP inspections.
- Manufactured to ISO 9001 Standards: Zotefoams plc, the manufacturer of T-FIT, operates under an ISO 9001-certified Quality Management System for foam production at its facilities in the UK, Poland, and the US. Covering key aspects of good manufacturing practices.
Why cGMP Compliance Benefits Your Business
Beyond meeting FDA regulations, cGMP compliance protects your business and customers:
- Product Quality: Guarantees that medicines meet required strength, purity, and quality.
- Brand Reputation: Builds trust with consumers and stakeholders.
- Risk Mitigation: Reduces the likelihood of recalls, lawsuits, or regulatory penalties.
Conclusion
cGMP compliance is the cornerstone of pharmaceutical manufacturing excellence. While processes and materials are crucial, choosing the right insulation can significantly impact your facility’s ability to meet these stringent standards. T-FIT Clean insulation, with its exceptional moisture and fungal resistance, low outgassing, and proven compliance record, is the ideal partner for clean manufacturing environments.
Ensure your facility is inspection ready. Choose T-FIT insulation as an essential component to achieving cGMP compliance.
Introduction
In controlled environments like cleanrooms, food and beverage facilities, and pharmaceutical manufacturing, maintaining optimal insulation performance is critical. However, one often-overlooked factor that can significantly undermine insulation efficiency is moisture penetration.
It has been shown that just 4% water absorption by insulation can lead to a 70% reduction in its thermal performance. Furthermore, a staggering 98% of insulation failures are due to water absorption/wicking. Failed or poor-performing insulation can lead to injury, increased energy use and product contamination.
This silent invader can lead to costly and potentially dangerous consequences, making moisture resistance a non-negotiable feature for high-performance insulation.
The Problem with Moisture
Moisture in insulation poses serious risks that go beyond reduced thermal efficiency. Here’s why it matters:
- Increased Thermal Conductivity: Water conducts heat about 20 times better than air. When moisture seeps into insulation materials, it raises the thermal conductivity, reducing the material’s ability to maintain desired temperatures. This compromises energy efficiency and increases operational costs.
- Corrosion Under Insulation (CUI): Trapped moisture can accelerate the corrosion of underlying pipe systems, leading to equipment failures and safety hazards.
- Bacterial Growth: Damp insulation creates a breeding ground for bacteria and mould, which can contaminate clean environments and jeopardize product safety.
- Structural Strain: As insulation absorbs moisture, its mass increases, putting additional pressure on pipe systems and structural components.
How T-FIT Insulation Addresses Moisture Issues
T-FIT insulation is designed to combat these challenges with advanced material technology that prevents moisture penetration. Here’s how it works:
- Closed-Cell Foam Structure: Unlike traditional insulation that relies on external cladding, T-FIT insulation uses closed-cell foam. This material inherently resists water absorption, maintaining its thermal properties and durability over time.
- High Water Vapour Diffusion Resistance: T-FIT boasts exceptional water vapour diffusion resistance (µ values). For example, a 6.35mm layer of T-FIT insulation at 23°C has the same resistance to water vapour transmission as 40 meters of still air at the same temperature. This barrier ensures that moisture stays out, even in humid conditions.
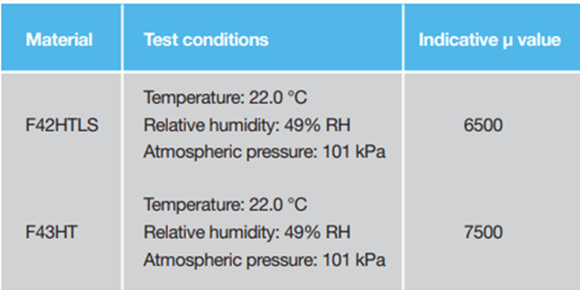
Why It Matters
Moisture in insulation doesn’t just lead to technical issues—it can also cause significant financial and operational setbacks. Energy losses, contamination risks, and the potential for equipment damage highlight the critical importance of selecting an insulation material that offers consistent moisture resistance.
While traditional insulation with aluminium cladding may claim high water vapour resistance, these properties depend on the cladding remaining intact. Any damage to the cladding can drastically reduce resistance, allowing penetration and absorption of moisture, and compromising performance over time. In contrast, T-FIT insulation’s closed-cell foam structure provides inherent moisture resistance that remains effective even under challenging conditions.
This durable design not only protects against moisture ingress but also ensures long-term reliability, making T-FIT a dependable choice for demanding environments. By prioritising moisture-resistant insulation like T-FIT, you safeguard your equipment, maintain product integrity, and achieve lasting cost efficiencies.
Introduction
In clean manufacturing environments—such as cleanrooms, pharmaceutical facilities, and food production plants—maintaining a sterile and contaminant-free space is essential. One of the most significant threats to these controlled settings is microbial contamination caused by fungal growth. The solution? Insulation materials designed to resist fungi and prevent mould growth.
Understanding the Threat of Fungal Growth
Fungi may seem like a minor issue, but in clean manufacturing environments, their impact can be devastating:
- Product Contamination: Mould and fungi can compromise the cleanliness of manufacturing areas, leading to contaminated products and costly recalls.
- Cleanroom Compliance Risks: Mould growth can jeopardize a facility’s compliance with strict regulatory standards, including cGMP, risking fines and operational shutdowns.
- Health Hazards: Airborne fungal spores can harm workers’ health and the quality of pharmaceutical or food products.
What Makes Insulation Vulnerable?
Many insulation materials have surfaces that trap debris, moisture, or nutrients, creating an ideal breeding ground for fungal growth. In warm, humid conditions—often present in food production facilities—fungi can quickly proliferate, threatening the integrity of the clean environment.
T-FIT: The Proven Solution for Fungus Resistance
T-FIT insulation is engineered to eliminate the risk of fungal growth, ensuring cleanliness and compliance. Here’s how it sets itself apart:
ASTM G21 Testing Excellence: T-FIT insulation has been tested for fungus resistance. The ASTM G21 standard exposes materials to five fungal species in high humidity (85%+) and warm temperatures (28-30°C) over 28 days. T-FIT consistently scores a mould growth rating of zero, indicating no visible fungal growth.
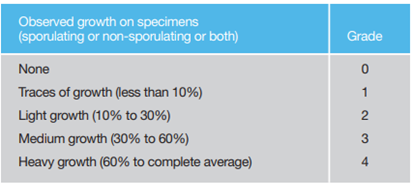
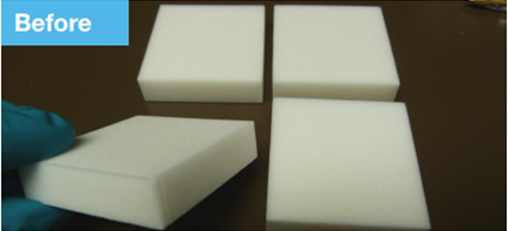
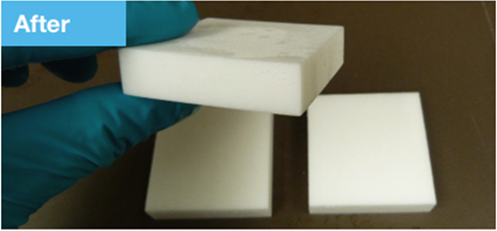
The images above show the foam samples before and after the test; as one can see the samples look as good as new, even after 28-days exposure to a variety of fungal spores in high humidity.
Smooth, Sealed Surfaces: Unlike porous insulation materials, T-FIT Clean insulation has a smooth, non-porous surface. This design prevents the accumulation of nutrients, debris, and moisture that fungi need to thrive.
Durability in High-Risk Environments: Even in challenging conditions, T-FIT insulation maintains its integrity, making it an ideal choice for environments with stringent cleanliness requirements.
Why Fungus Resistance Matters
Choosing fungus-resistant insulation isn’t just about maintaining a clean facility—it’s about ensuring operational efficiency and compliance with industry standards.
Controlling fungal growth protects:
• Product Integrity: Prevents costly contamination and production delays.
• Compliance: Reduces the risk of failing inspections and ensures adherence to cGMP and other industry guidelines.
• Workplace Health: Minimises the risks of mould-related health issues for employees.
Conclusion
In environments where cleanliness and sterility are paramount, fungal growth is a risk you cannot afford to ignore. By choosing T-FIT insulation, you gain a trusted partner in maintaining a contaminant-free space. With its proven fungus resistance, smooth surface, and exceptional performance in demanding conditions, T-FIT insulation ensures your facility stays clean, compliant, and efficient.
Don’t let mould compromise your operations. Choose insulation that works as hard as you do—choose T-FIT.
In industrial settings, safety is extremely important, especially when dealing with high temperature processes. Contact burns are a serious risk, even if someone only touches a hot surface for a very short time as it can lead to significant injuries, including first- and second-degree burns, which can result in pain, time off work, and even permanent damage.
Traditional insulation methods often do not provide adequate protection, leaving workers vulnerable to these types of injuries and putting companies at risk of breaking important safety regulations. T-FIT insulation addresses these challenges by lowering contact surface temperatures on hot pipes and equipment, making workplaces considerably safer.
Proven Results
T-FIT insulation has been tested thoroughly and has consistently proven effective at keeping contact temperatures below dangerous levels, even under the toughest conditions. Using advanced tools such as a thermesthesiometer (a device that measures how hot a surface feels to the touch), we measured the reduction in surface temperature provided by T-FIT insulation. These results show that T-FIT can lower temperatures enough to significantly reduce the risk of burns.
For example, during testing:
Product (all 6.35 mm thick) | Maximum operating temperature stated on data sheet (°C) | Actual temperature of mandrel (°C) | Maximum 5 second contact temperature recorded (°C) |
---|---|---|---|
T-FIT Clean | 160 | 159 | 33 |
T-FIT Hygiene | 145 | 147 | 35 |
Maximum recorded contact temperature for T-FIT Products
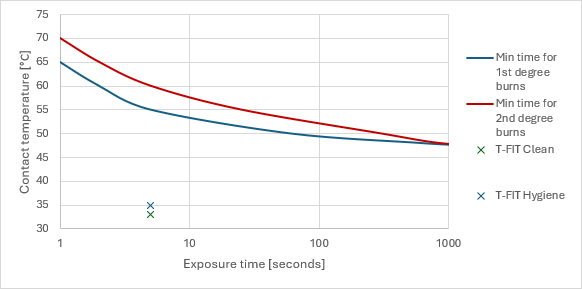
These temperatures are much lower than the level that causes first-degree burns, providing facility managers with peace of mind and helping them meet important safety standards. Keeping the temperatures below these levels means that workers are far less likely to suffer injuries from accidental contact with hot surfaces, making their work environment significantly safer.
Impact: A Safer Workplace
By using T-FIT insulation, industrial facilities can create much safer environments for their workers. Lower contact temperatures mean there is a much lower chance of accidents and injuries, which in turn helps to improve safety records and reduces the risk of legal or financial issues for employers. When safety is improved, everyone benefits: workers feel more secure, productivity increases, and the company avoids costly downtime and liability issues.
T-FIT insulation is also easy to install, which makes it a convenient solution for improving safety without requiring major disruptions to facility operations. Its effective burn prevention capabilities provide ongoing protection for employees, demonstrating the company’s commitment to a safe working environment.
Real-World Application
In a recent project, T-FIT insulation was used in a high-temperature processing facility, and the results have been impressive. Due to the low profile of T-FIT, it maximized coverage and allowed for insulation of parts, including valve boxes, that are often left uninsulated and pose a significant safety risk. After the installation, the facility reported fewer burn-related accidents, creating a much safer work environment and reducing the need for extra safety measures. Workers felt more comfortable and confident, knowing that the risk of burns had been greatly reduced, which also helped improve morale and overall productivity.
“We are very pleased with the results of installing T-FIT Hygiene pipe insulation in our brewery. It has made a huge difference into the safety of our staff while also improving the hygiene and aesthetics of the pipework. T-FIT is easy to install, maintain, and clean, and it looks great. The flexibility in which it can be supplied makes it such a great product for us and it has solved all the problems we had with our old fibre insulation system.” – Lewis McLeavey, Engineering Leader, Meantime Brewery
This real-world example shows how T-FIT insulation can make a real difference in industrial environments. By lowering contact temperatures and preventing burn injuries, T-FIT insulation helps facilities meet safety standards, protect workers, and reduce the risk of accidents and liability.
Leadership in Energy and Environmental Design (LEED®) is a globally recognized green building certification system developed by the U.S. Green Building Council (USGBC). LEED evaluates the sustainability of buildings based on various categories, promoting environmentally responsible and resource-efficient construction. Attaining LEED certification can significantly boost the environmental credibility of a building project, offering both economic and ecological benefits.
Within the LEED framework, buildings are assessed across nine categories, each containing prerequisites and credit scoring opportunities. T-FIT® Technical Insulation products offer several sustainability benefits that may help contribute to earning LEED points in key areas.
What are the categories where T-FIT can contribute towards LEED Certification points?
Energy and Atmosphere (EA):
T-FIT is able to play a key role in contributing to the Minimum Energy Performance prerequisite. This is achieved by supporting energy savings in pipework and HVAC systems, which helps promote energy efficiency and reduces greenhouse gas emissions. In terms of credits, T-FIT® can contribute to the Optimize Energy Performance category, where it can help earn between 1 and 25 points. T-FIT enables efficient energy savings, even in difficult-to-access areas, thereby improving overall building energy performance.
Materials and Resources (MR):
In the Building Product Disclosure and Optimization – Material Ingredients category, T-FIT can help contribute to 1-2 points by being free from substances listed on the REACH Substances of Very High Concern (SVHC) list. This can help to earn credits through the ‘International Alternative Compliance Path.’ Additionally, T-FIT supports the Construction and Demolition Waste Management category, potentially contributing to 2 points by minimizing waste through its durability and ease of installation. The long lifecycle of T-FIT reduces the need for frequent replacement, thus lowering the amount of material waste generated during construction and demolition.
Indoor Environmental Quality (EQ):
T-FIT can contribute to the Low-Emitting Materials credit, where it can help earn 1-3 points. The product produces very low volatile organic compounds (VOCs), meeting stringent standards, including the California Department of Public Health regulations, a standard for evaluating building and interior products for low chemical emission. This makes T-FIT ideal for improving indoor air quality. Furthermore, T-FIT helps contribute to the Indoor Air Quality Assessment credit (1-2 points) by ensuring better indoor air through minimal emissions of VOCs, carbon monoxide, and ozone. This enhances the health and comfort of building occupants.
Sustainable Insulation:
In the Building Life-Cycle Impact Reduction category, T-FIT can contribute towards earning 1-4 points by offering enhanced durability and energy efficiency. Its long-lasting performance helps reduce a building’s global warming potential, cutting down on energy and material consumption over time. T-FIT insulation helps a building meet its sustainability goals, both in terms of environmental performance and lifecycle impact reduction.
Conclusion
By integrating T-FIT Insulation into your building project, you can enhance energy efficiency, reduce waste, and improve indoor air quality, all while supporting the pursuit of LEED certification. Although the use of T-FIT does not guarantee certification, it offers significant contributions towards fulfilling the prerequisites and earning valuable LEED credits, supporting your goal of creating a sustainable and environmentally friendly building.
For more details on how T-FIT® can contribute to your specific project’s LEED certification, please contact our team.
Introduction
Infosys Technologies is an Indian multinational information technology company that provides business consulting, information technology, and outsourcing services. Headquartered in Bangalore, the company has a strong commitment to sustainability and operational efficiency, which drives its interest in optimizing the performance of its infrastructure, including solar water heating systems and heat pumps on the roof of the building.
To improve the efficiency and longevity of their solar water heating systems and heat pumps, with a working temperature of 80 to 95°C, Infosys Technologies wanted to invest in insulation and started a comparative trial between two insulation materials: T-FIT Insulation and Nitrile Rubber.
When selecting pipe insulation, the choice between materials can significantly impact performance, efficiency, and longevity. This trial was conducted over two years, and the results were eye-opening.
Comparative Analysis
Performance of Nitrile Rubber
Nitrile Rubber is widely known for its insulating properties, typically has a temperature range of -35°C to +120°C. Initially, it seemed like a suitable choice for insulating solar water heating systems and heat pumps.
However, upon reaching the two-year mark, significant deterioration was observed in the Nitrile Rubber material. The insulation began to show signs of wear and tear, impacting its ability to maintain effective insulation. This degradation leads to a decline in the performance of the solar water heating systems and heat pumps, as consistent insulation is crucial for their efficiency.
Infosys Technologies noted these issues, highlighting the need for a more durable and reliable insulation material. The performance of Nitrile Rubber, while initially satisfactory, proved to be unsustainable in the long term.
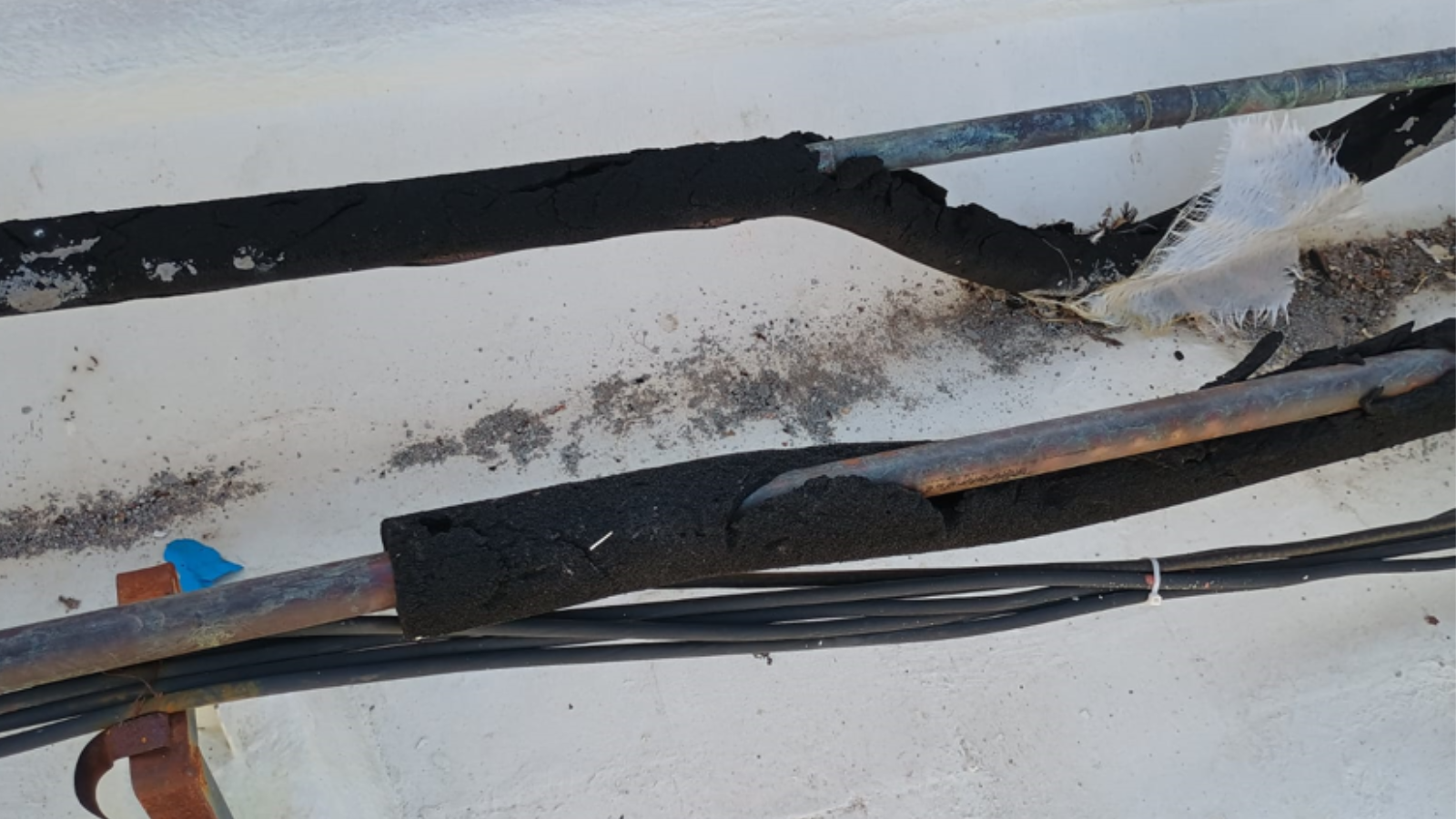
Performance of T-FIT Insulation
T-FIT Insulation represents a cutting-edge solution that redefines pipe insulation standards. Used in the same conditions as Nitrile Rubber, not only met but exceeded expectations. It demonstrated remarkable stability and effectiveness within the given temperature range of 80 to 95°C.
The standout feature of T-FIT Insulation was its durability. Over the two-year period, T-FIT Insulation maintained its excellent performance. Unlike Nitrile Rubber, there were no significant signs of wear and tear. This consistent performance ensured that the solar water heating systems and heat pumps operated at optimal efficiency throughout the duration of the study.
Infosys Technologies was highly impressed with T-FIT Insulation. The material’s ability to maintain its insulating properties without significant degradation led to a high level of satisfaction. Based on its superior performance, Infosys Technologies placed a repeated order for T-FIT Insulation, underscoring their confidence in the material.

Conclusion
The two-year live comparison between T-FIT Insulation and Nitrile Rubber provided clear insights into the superior performance of T-FIT Insulation. Its ability to maintain insulation effectiveness and durability over a prolonged period makes it a more reliable and cost-effective solution for long-term projects. Infosys Technologies’ decision to place a repeated order underscores the material’s reliability and performance excellence.
This comparative study highlights the importance of choosing the right insulation material for solar water heating systems and heat pumps. T-FIT Insulation stands out as a superior choice, ensuring consistent performance and longevity, ultimately leading to more efficient and reliable systems.
In the dynamic landscape of industrial insulation, where every decision shapes operational efficiency and longevity, the choice between conventional “Pipe in Pipe” format insulation and the revolutionary T-FIT® Insulation system carries significant weight. In this comprehensive exploration, we’ll delve deeper into the nuances of each system, highlighting how T-FIT redefines insulation standards and offers unparalleled advantages for modern industrial applications.
Embracing Innovation: The Evolution of Insulation Systems
Traditionally, the “Pipe in Pipe” insulation relies on an inner pipe for media transport, surrounded by an outer jacket filled with open-cell insulation. While effective, this approach often posed challenges related to moisture management and maintenance. Enter T-FIT, a unique closed-cell insulation system designed to address these shortcomings. Unlike its predecessors, T-FIT eliminates the need for an outer water vapor barrier, simplifying installation and enhancing performance. Its modular design, complete with moulded fittings, insulation boxes, installation tape, and sealant, represents a significant leap forward in insulation technology, offering a well-rounded solution tailored to the demands of modern industry.
Streamlined Installation: Efficiency From Start to Finish
The installation process is a crucial aspect of any insulation system, with implications for both time and cost. Traditionally ‘pipe in pipe’ insulation often arrives in cumbersome, lengthy sections, susceptible to damage during transport. On-site assembly through welding or bolting further complicates matters, while the need for custom cutting adds time and labour expenses. In stark contrast, T-FIT arrives in meticulously packaged lengths, safeguarded in antistatic plastic bags within corrugated cartons to ensure product integrity. With pre-installed closure tape and moulded fittings for various components, T-FIT streamlines the installation process, reducing downtime and minimising associated costs. Its user-friendly design and comprehensive installation accessories make it the preferred choice for industries seeking efficiency without sacrificing quality.
Simplified Maintenance: A Focus on Accessibility and Visibility
Maintenance is a cornerstone of operational reliability, yet traditional insulation systems often hinder accessibility and visibility, leading to potential issues with corrosion, efficiency loss, and performance degradation. In “Pipe in Pipe” setups, the condition of inner insulation remains obscured, making it challenging to detect and address maintenance issues promptly. T-FIT revolutionises the maintenance paradigm with its easy removal and reinstallation. By providing visibility into insulation condition and facilitating quick inspections, T-FIT empowers maintenance personnel to identify and rectify issues proactively, ensuring uninterrupted functionality and extending the lifespan of critical assets.
Unparalleled Performance: Consistency and Reliability Redefined
Performance discrepancies are a common concern with traditional insulation systems, where thermal efficiency often depends on hidden insulation types and maintenance-related welding introduces uncertainties. T-FIT sets a new standard for performance consistency and reliability. Its closed-cell insulation construction ensures uniform thermal properties, while easy access for maintenance and inspection promotes proactive intervention and quality control. By prioritising transparency and ease of maintenance, T-FIT delivers consistent performance excellence, making it the preferred choice for industries where reliability is non-negotiable.
The Future of Insulation: An Ideal Shift in Industry Standards
As industries evolve and technology advances, insulation systems too. must evolve to meet the evolving demands of modern industrial applications. T-FIT represents a paradigm shift in insulation technology, offering a comprehensive solution that addresses the challenges of traditional systems while setting new benchmarks for efficiency, reliability, and performance. By embracing innovation and prioritising user-centric design principles, T-FIT paves the way for a future where industrial insulation is synonymous with efficiency, reliability, and sustainability.
In conclusion, the choice between traditional “Pipe in Pipe” insulation and T-FIT is more than a matter of preference; it’s a strategic decision that can impact operational efficiency, reliability, and longevity. With its innovative features, streamlined installation process, simplified maintenance requirements, and unparalleled performance, T-FIT emerges as the undisputed champion in industrial insulation, unlocking new levels of efficiency and reliability for critical piping systems.
While standards and specifications abound when it comes to the design features, apparel and operator protocols necessary to minimise particulates as a contaminant in cleanrooms, there is little or no formal consideration of the part played by materials such as those used for insulation. Here, Mike Rust, Global Development Manager – T-FIT® Insulation at Zotefoams plc, considers the issues and describes a test protocol developed to measure the particulate contribution of three different types of insulation during typical cutting and fitting operations within a cleanroom.
Wherever cleanroom manufacturing happens, be it for pharmaceuticals, biotechnology or semiconductors, the environment must be designed to ensure the safety and quality of products. Cleanroom design minimises the introduction and circulation of potential contaminants, with control of particulate emissions essential to maintaining a secure, clean environment.
The construction of the cleanroom shell — the walls, floors and ceilings — is subject to exacting engineering standards and specifications to maintain air quality in terms of particulate release. In 2016, ISO 14644, the recognised standard for cleanrooms, was expanded specifically to include the “assessment of suitability for use of equipment by airborne particle concentration” — although it did not extend to such important matters as the selection, testing or ease of cleaning of selected materials.
Thermal insulation — important but overlooked
Amid all the attention paid to preventing, monitoring, and controlling particulates, one important aspect is often overlooked: the impact on particulate levels of the thermal insulation that controls the surface temperatures of process pipework and HVAC equipment in and around cleanrooms while conserving energy and providing personal protection for operators.
Whatever type of insulation is selected, during installation it will have to be cut to size and very likely manipulated to fit complex pipework runs in tightly confined spaces — all happening in situ. Post-installation, thermal insulation is not simply ‘fit and forget’: it is typically checked regularly as it is removed to facilitate pipeline maintenance and repair. And it is during removal that traditional thermal insulation products can pose the most danger in terms of emitting potentially hazardous particulates into the cleanroom environment.
Absence of independent testing
So far as we can ascertain, there are no recognised independent tests that compare the particulate-emission performance of different insulation materials commonly used in a cleanroom — a situation that is no help to those charged with specifying appropriate insulation solutions.
With all the above in mind, Zotefoams therefore commissioned Occhnet, a leading occupational hygiene consultancy based in the UK, to design and conduct an independent test of T-FIT Clean foam insulation, produced from Zotefoams’ ZOTEK® F high-performance PVDF closed cell foam. T-FIT Clean’s performance was tested against two traditional insulation products, manufactured respectively from foil-backed stone wool and flexible open cell melamine with a PVC jacket. The testing measured the indicative concentrations of particulates released into the air during cutting of the material.
The testing replicated the worst-case scenario — that of operators slicing and/or cutting the insulation within the cleanroom —simulating cutting-to-size operations during installation and replacement maintenance.
The test
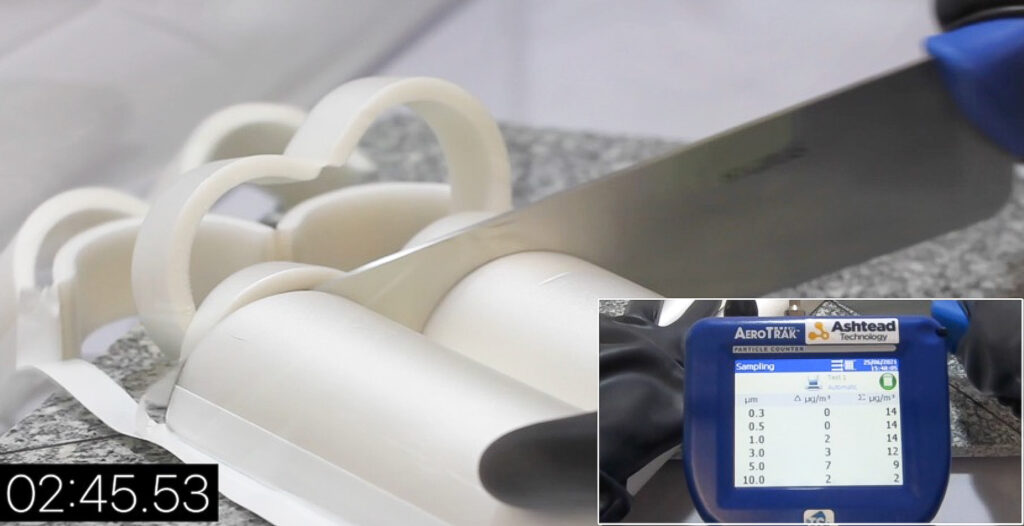
Each sample insulation material was placed into a sealed glovebox (see Figure 1 above) containing a particle counter. This ensured that, once the test samples and testing equipment were inside, no further particulate could be introduced. The glovebox did not contain an air exchange or filtering system.
To allow for the stabilisation of the background particulate reading, the procedure started with a two-minute static period where there was no movement within the glovebox. Once that static period was completed, each test piece was subjected to three cuts at 90° and three at 45°. Cutting lasted one minute in duration, followed by a further two-minute static period.
To measure any increases in background particles within the glovebox, differential µg/m3 readings were taken at particulate sizes of 0.5, 1.0, 3.0, 5.0 and 10.0 µm, at a flow rate of 2.83 l/m.
The results
Measurement and comparison between the three materials produced results worthy of consideration by those charged with cleanroom design and operation.
T-FIT Clean: As Figure 2 below shows, the particle count fell steadily through the first two minutes of the static period. During cutting and manipulation and also in the final two-minute static period there is a continued gradual decrease in particle count, indicating that T-FIT Clean does not emit particles within the measured particle size (0.3 to 10 micron). Occhnet concluded that “there was no detectable release of particulate during the cutting period.”
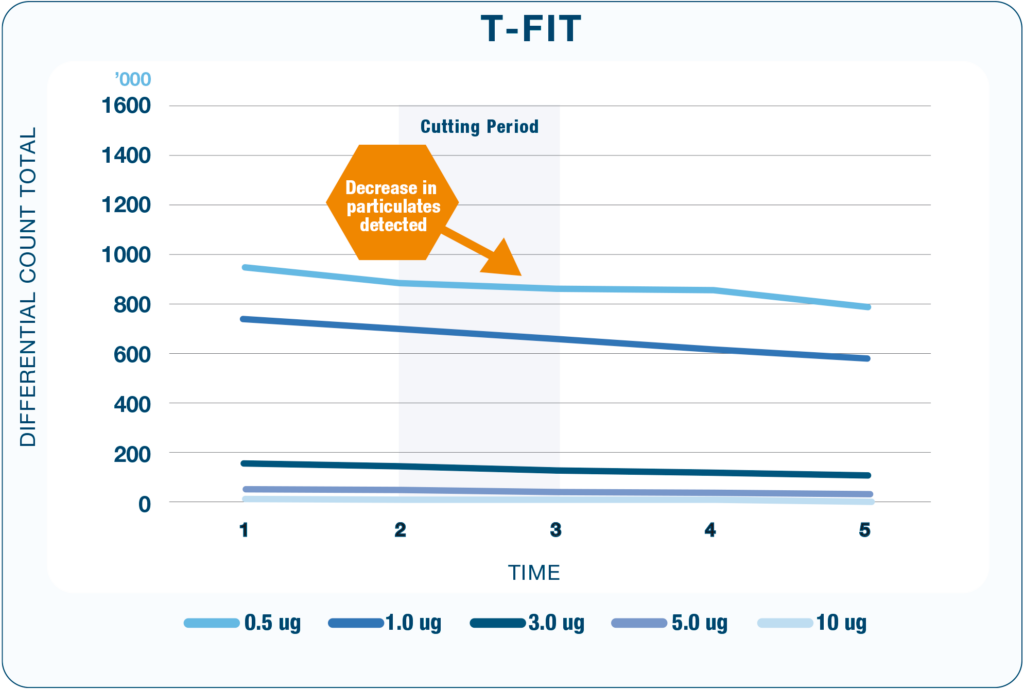
Flexible open cell melamine: When this typical melamine product, often installed in cleanrooms, was cut and manipulated, there was a significant increase in background particulates, indicating the materials added large amounts of particulates into the environment even before it is cut (see Figure 3 below where the particulate count starts at 2 million). Occhnet observed that a clean cut was difficult to achieve without compressing the material, which released air from the open-cell construction, and that this coincided with the rise in particulate count.
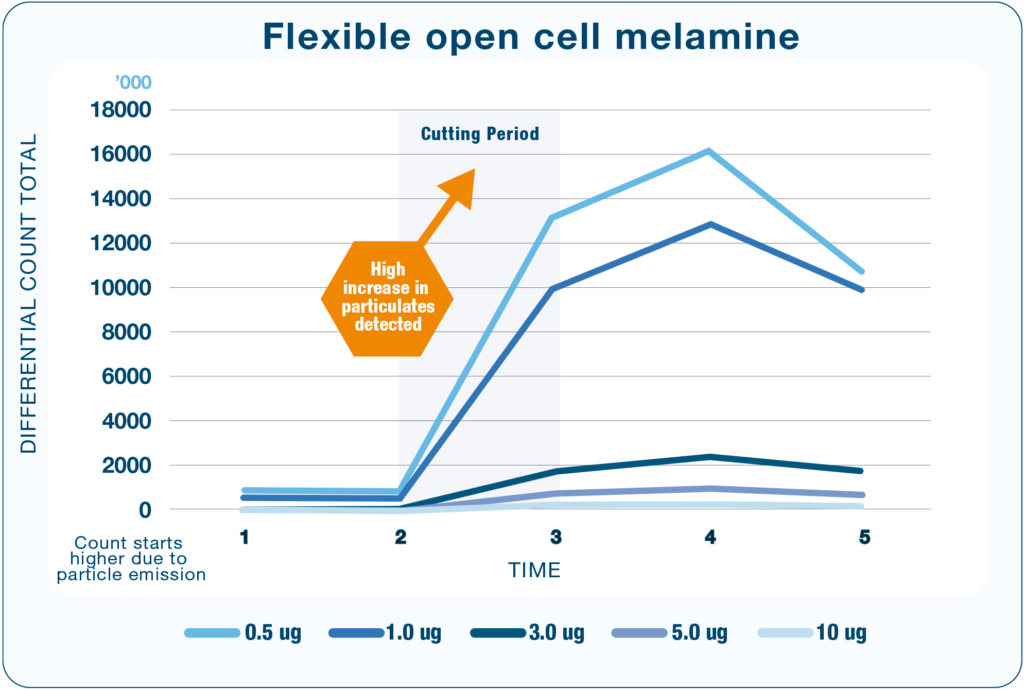
Foil-backed stone wool material: The particle count was stable during the static period but as soon as cutting commenced the particle count rose significantly, and particularly for larger particles (Figure 4 below). According to Occhnet, while a clean cut was possible without compressing the sample, “the material appeared friable and the rise in count was indicated to be associated with the cutting of the material.”
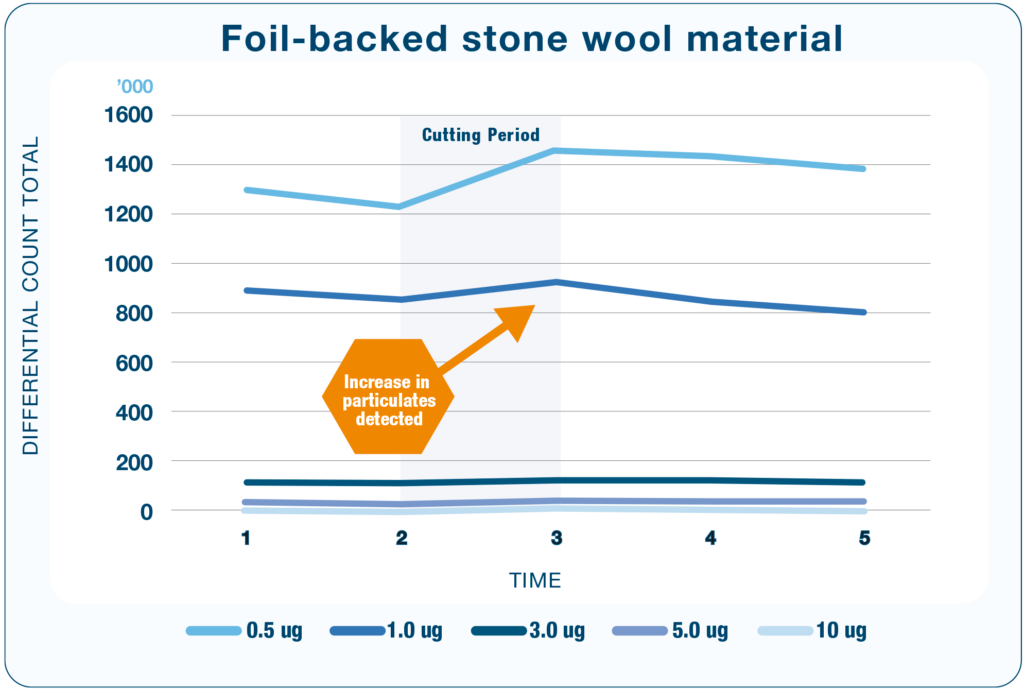
It should be noted that this material incorporates a glue binding the fibres together, which is likely to deteriorate when the material is used in high-temperature applications, raising the prospect of particulate emissions increasing over time.
A unique manufacturing process
— Why T-FIT outperforms the competition
T-FIT Clean’s best-in-class control of particulate emission lies in its unique three-stage foam manufacturing process that uses pure nitrogen as a foaming agent and produces materials with a remarkably consistent, fine closed cell structure.
In Stage 1, pure PVDF polymer is extruded into a solid slab, then irradiated to create chemical bonds that join the polymer chains (crosslinking). This results in excellent thermal stability, high strength and toughness compared to non-crosslinked materials, and crosslinking via irradiation also prevents the shrinkage that is often associated with thermoplastic materials. Stage 2 applies extremely high pressures and temperatures to dissolve the nitrogen gas into the slabs. In Stage 3, the nitrogen-saturated slabs are put through a second, high-temperature, lower-pressure cycle where the pressure is gradually released to allow the free expansion of the material into sheets of foam.
The result is a fine, completely closed cell structure that demonstrates exceptional performance across the board, not just in limiting particulate emissions but on all measures of cleanroom insulation efficiency. T-FIT Clean is also highly resistant to bacteria and mould growth and its ASTM G21-tested performance on zero fungal growth brings long-term protection against the risk of product contamination. Compared to open cell materials, T-FIT more effectively limits moisture and gas penetration because there is no continuous network through which substances can travel.
For high-temperature environments, T-FIT Clean offers exemplary fire safety credentials. Rated 0/0 (Flame-Spread Index/Smoke Development Index) at 3mm according to ASTM E84 for surface burning characteristics of materials, T-FIT Clean delivers the lowest flame, smoke and toxicity rating of any polymer/elastomer insulation.
A wide temperature operating range — from -80°C to +160°C — combined with the durability of the material ensures thermal performance remains unimpaired in the long term, even where repeated cycling between chilled process temperatures and high cleaning temperatures (clean in place, sterilise in place) is involved.
Test the best with a free trial installation
T-FIT offers customers the opportunity to ‘put the best to the test’ for themselves under ‘real-world’ cleanroom conditions with a free trial installation of T-FIT Clean. To request a trial, or for further information about the comparative testing, contact us at t-fitsales@zotefoams.com or visit us at https://t-fit.org
Recently released results from a testing programme designed to determine the service life of T-FIT Clean and T-FIT Hygiene PVDF foam insulation have revealed some surprising findings.
With sustainability now a near-universal priority, being able to give potential users an indicator of use phase performance and longevity of a product is an important factor and one which also helps determine Total Cost of Ownership (TCO).
T-FIT, a business unit of Zotefoams plc, therefore devised a test programme based on heat-ageing to compare its T-FIT Clean and T-FIT Hygiene modular insulation products with an alternative EPDM-based foamed rubber material, adopting thermal conductivity as the best indicator of the materials’ respective longevity in use. Thermal conductivity measures how easily heat travels through materials by conduction and is recognised as a critical feature of effective insulation: the lower a material’s thermal conductivity, the better the performance.
Samples of Zotefoams’ ZOTEK® F PVDF foam – from which T-FIT Clean and T-FIT Hygiene are produced – and a sheet of EPDM-based foamed rubber insulation were placed in an oven set at 145°C for a period of 30 days. The thermal conductivity of the materials was measured before and after testing.
The results (see below) clearly demonstrated T-FIT’s superior performance. After just 30 days, the thermal conductivity performance of the EPDM sample had deteriorated by 8%; conversely the ZOTEK F samples showed an improvement in thermal conductivity.
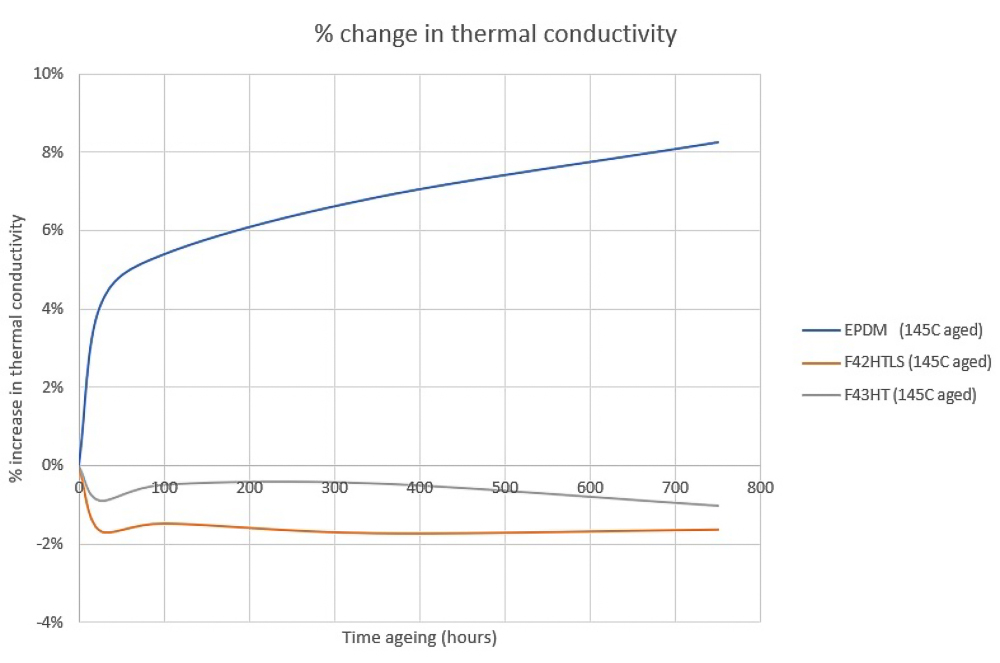
Mike Rust, T-FIT Global Development Manager, says: “Longevity is a key component of sustainability, a major focus for prospective customers. As a raw material, we know that ZOTEK F has outstanding longevity, with high resistance to UV and to aggressive chemicals but, understandably, there is interest in what impact, if any, simulated operating conditions have on the material and also how T-FIT performs compared to alternatives. The best way to demonstrate this is through a head-to-head test.
“Extending the testing to 30 days far exceeds the 72 hours required by EN 14707, the European standard that determines the maximum service temperature of thermal insulation products. It’s worth noting, too, that the thermal conductivity of the EPDM-based material begins to deteriorate almost immediately, increasing by over 5% within the relatively small 72-hour window.”
T-FIT is continuing the testing programme to monitor the materials’ performance under even longer exposure to high temperatures, with results available in due course.
T-FIT technical insulation is designed specifically for demanding applications in pharmaceutical, biotech, semiconductor, food, beverage and general processing industries. T-FIT Clean, the flagship product, was developed for cleanroom applications and remains the only insulation solution that complies with all internationally recognised cleanroom standards. T-FIT Hygiene is ideal for aseptic areas in food and beverage, dairy, and personal care. The combination of Zotefoams’ unique three stage manufacturing process and the natural properties of the high-grade PVDF polymers creates a pure, high-performance modular technical pipework insulation solution that delivers excellent thermal resistance, is heat-retardant and UV- and fire-resistant.
Manufactured from Zotefoams’ ZOTEK F closed cell PVDF foam, T-FIT Clean and T-FIT Hygiene are highly resistant to bacteria and mould growth, meets and exceeds the industry-standard ASTM G21-15, are particulate-, dust-, fibre-free- and emit near-zero levels of VOCs. They also withstand the rigours of routine deep cleaning processes with industrial strength chemical agents, disinfectants, and sanitisers.
T-FIT is designed for fast, tool-free installation reducing labour costs, downtime and – most importantly – the Total Cost of Ownership.
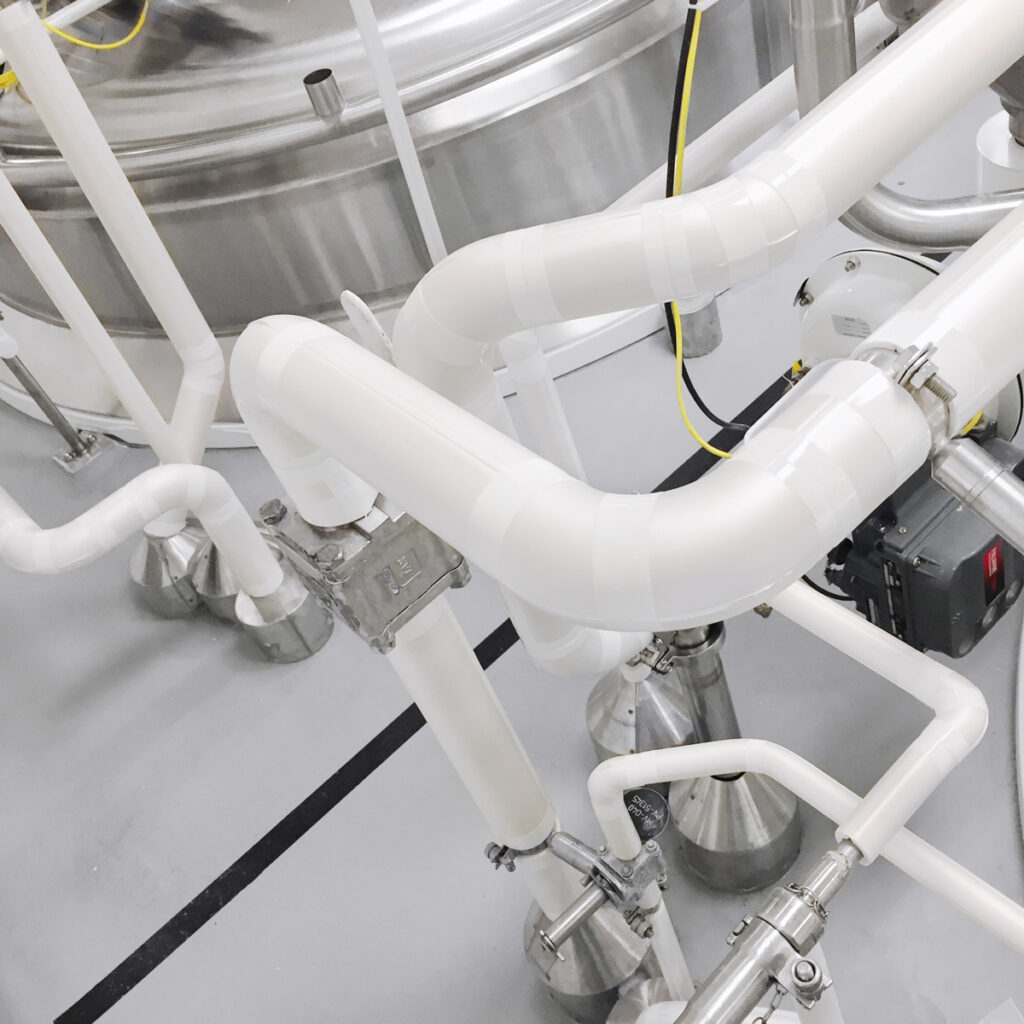
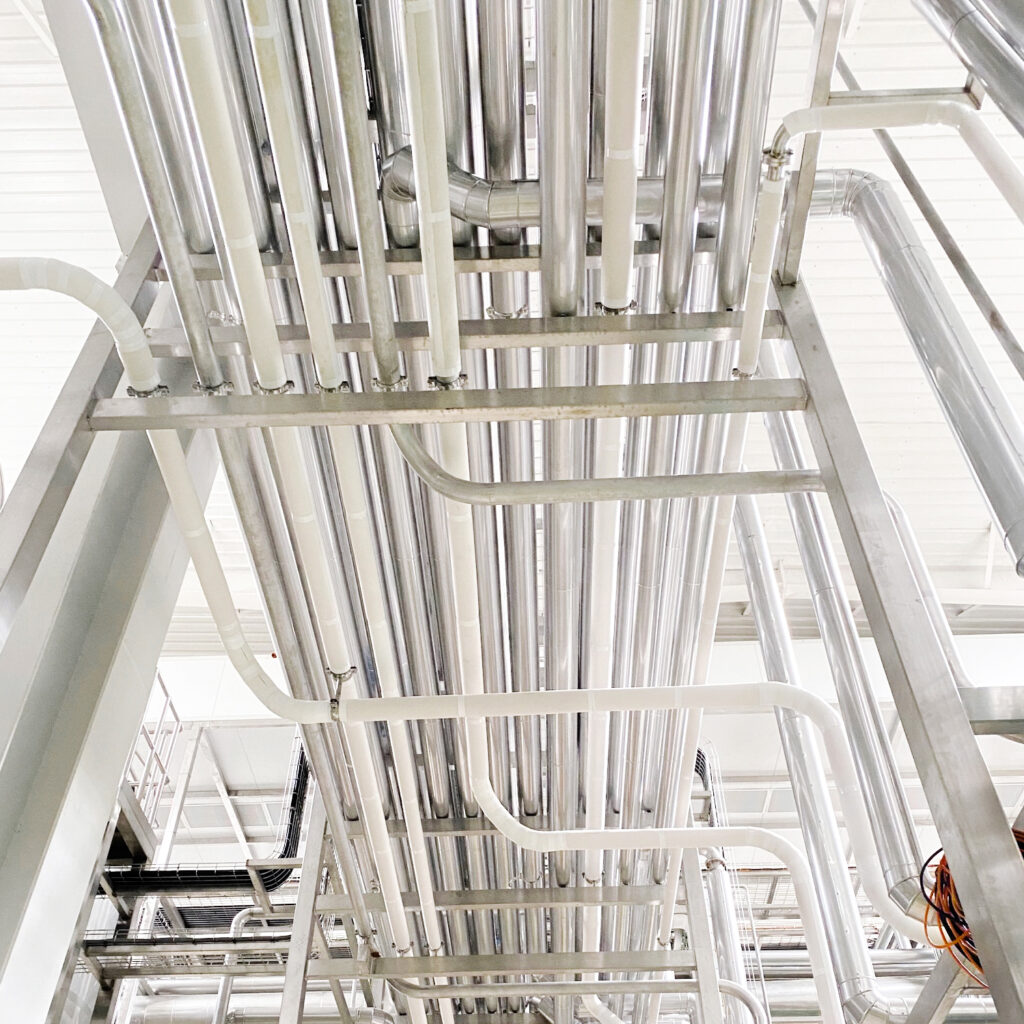
Routine deep cleaning of cleanroom and other aseptic environments is critical to maintaining product quality and protecting consumers in food and beverage, semiconductor, and pharmaceutical manufacturing. The use of industrial-strength chemical agents, disinfectants and sanitisers where protocols dictate can result in deterioration of traditional insulation materials, leading to waste and costs associated with replacement.
While different areas of the cleanroom require different cleaning regimes, there are some that call for special attention. HVAC ducting and pipework, for example, are often shielded with thermal insulation material that can attract contaminants. The remedy is to clean using aggressive cleaning agents but these can cause some traditional insulation materials to break down. Open cell insulation materials are particularly susceptible to damage and deterioration because the cladding systems employed to protect them often fail to prevent the cleaning agents wicking into the structure of the insulation, accelerating wear and tear and eventually causing it to fail.
Closed cell – a better solution
Closed cell foam insulation such as T-FIT® Clean offers a much better solution. Manufactured from Zotefoams’ high-grade polyvinylidene fluoride (PVDF) polymer using Zotefoams’ unique high-pressure autoclave, clean technology process, T-FIT Clean features a fine, closed cell foam structure that is inherently hydrophobic, and highly resistant to chemical cleaning agents.
To provide objective evidence of T-FIT Clean’s ability to withstand aggressive cleaning agents, T-FIT commissioned Independent Polymer Technology to conduct intensive testing[1] of samples of the insulation, based on the ASTM D543 chemical patch test, acknowledged as the most appropriate method for evaluating the resistance of plastics to chemical reagents.
The samples tested: So that all aspects of the insulation were evaluated, T-FIT provided Independent Polymer Technology with samples of the closed cell PVDF sheets from which T-FIT Clean is manufactured, the finished tubular components, and the PVDF tape used during installation.
The cleaning agents tested: Six commonly used cleaning agents were tested:
- P3-mip GEL caustic gel
- Topaz MDI alkaline foam cleaner
- Topaz AC2 liquid acidic detergent
- Spor-Klenz RTU 6525-08 EC
- CleanGuard 4 Alpha trigger spray sterile
- CleanGuard 3 Beta trigger spray sterile
Test methods
To establish reference data, before testing each specimen was visually examined and, to determine adhesion, the PVDF tapes were subjected to tensile and 180-degree peel strength testing. They were then subjected to a far greater exposure to cleaning agents than would occur in practice. Each set of specimens was covered with cotton cloths soaked in the cleaning agent being tested, after which the cloths were covered with plastic sheets and left for seven days. During this period, they were monitored and re-wetted if necessary to ensure continuous exposure. At the end of the test the cloths were removed and the specimens examined closely for any signs of adverse effects including softening, discolouration, cracking or blistering.
The results
Figure 1 below shows a selection of samples after seven days’ exposure to, in this case, Topaz AC2 liquid acidic detergent. There is no visible evidence whatever of any degradation. The same absence of deterioration and robust performance was noted for each of the T-FIT Clean samples tested.
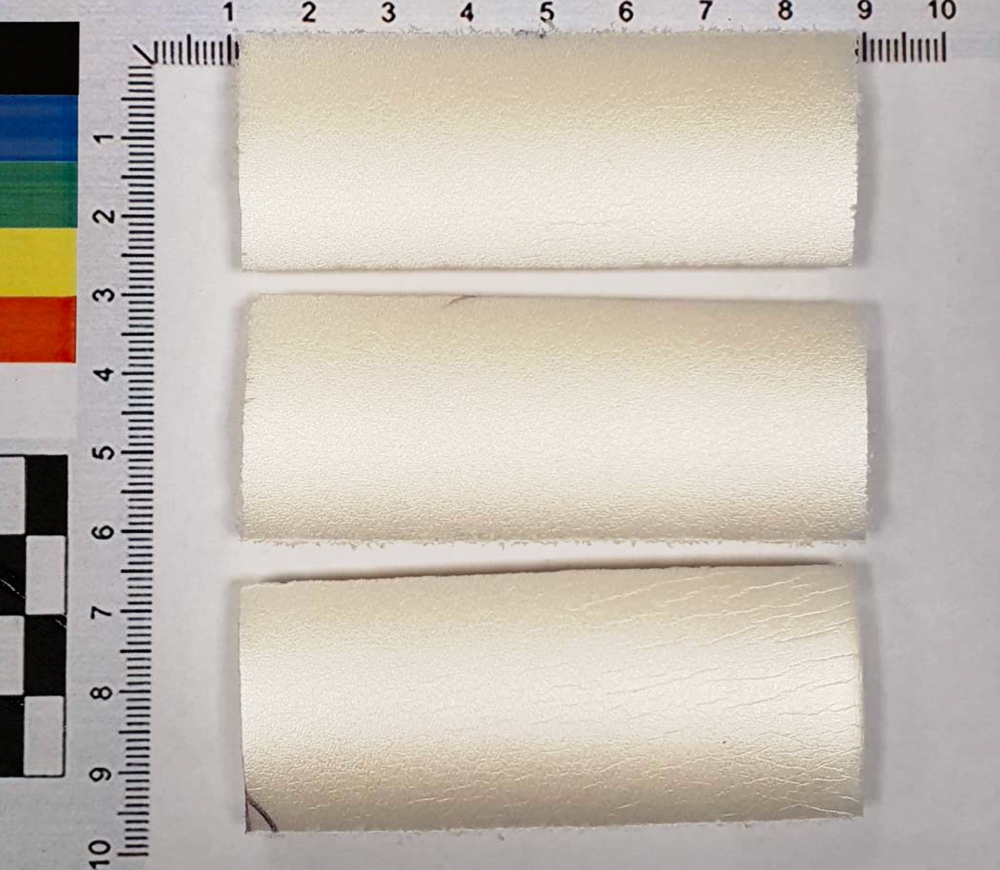
Fig 1: T-FIT Clean tube sections after seven days’ exposure to Topaz AC2 liquid acetic detergent.
More information on the testing process is available at https://zote.info/3HsAiiz
T-FIT Clean – outperforming the competition
With an operating range of -80°C to +160°C (effective up to 158°C steam pressure at 5 bar), T-FIT Clean is suitable for both chilled and hot processing applications. A single high-performance insulation solution can therefore be used throughout a cleanroom, its ultra-slim 6.35mm profile taking high-performance insulation into even the tightest spaces.
For fast, tool-free installation plus a long maintenance-free service life, the robust range includes products that can insulate pipework incorporating straight runs, elbows and T-sections with clamshell closures. T-FIT Clean is also available in sheet form for installation around tanks, vessels and ducting.
The cleanroom insulation solution of choice since 2008, T-FIT Clean is based on ZOTEK® F42 HT LS high-performance foam, the only foam compliant with the FM4910 Global Cleanroom Materials Protocol. T-FIT Clean has consistently outperformed the competition in the most demanding cleanroom and manufacturing environments and remains the only insulation solution that complies with internationally recognised cleanroom standards.
[1] Detailed information on the testing process is available at https://zote.info/3HsAiiz
WHY LOOKING BEYOND R-VALUES YIELDS BIG INSULATION BENEFITS
Ask most engineers how they measure the performance of thermal insulation and it’s almost certain they’ll reply, “Using the R-value, of course.” It’s an answer that’s virtually hard-wired into them. So it’s no surprise that “What’s the R-value?” is guaranteed to be one of their first question in any sales negotiation — certainly in my experience, and that of many colleagues.
R-values are the received wisdom for evaluating thermal insulation efficiency, but — as is often true of received wisdom — they don’t tell the whole story. In fact, they might even be misleading, which matters when governments around the world are setting ambitious targets for carbon reduction, and fit-for-purpose thermal insulation has never been more important.
An imperfect ratio
There are several reasons why R-values alone cannot provide a true and accurate measurement of how modern-day insulation should be chosen. The first is the formula on which the R-value calculation is based — the thickness of the insulation divided by its thermal conductivity. It’s a simple measure, according to which the thicker the insulation, the higher the resulting R-value and — supposedly — the better the product’s performance. It’s a simple, but imperfect, ratio, as I will explain. The second reason is that today’s thin-wall thermal insulation materials are by many measures equally, if not more, efficient than their bulkier competitors.
This case to look beyond R-values alone becomes stronger when you consider that the base calculation on which they are based is arguably outdated. It has been in place — unmodified and often unquestioned — for decades, and dates from the time when fibre-based products dominated the market. Due to the manufacturing process, these generally had a minimum thickness of 1” — with the result that building codes in many countries fail to take into account the advent of thin-wall materials, and so do not reflect the current state of insulation technology.
Missing the point
In my view, basing insulation purchasing decisions on R-values alone misses the point about why we insulate pipework in the first place — which is to reduce heat loss (or heat gain in cold-side applications). Change the focus, evaluate insulation performance by how effectively it performs these critical functions, and some interesting results emerge, as the following evaluations — all conducted under ISO 12241:2008 — demonstrate.
Consider a 2”NB pipe running at a line temperature of 302°F, with ambient conditions at 77 °F. Uninsulated, heat loss will be 359 BTU/h.ft, but install modern thin-wall insulation just 1/8” thick and heat loss falls dramatically — by 50%.
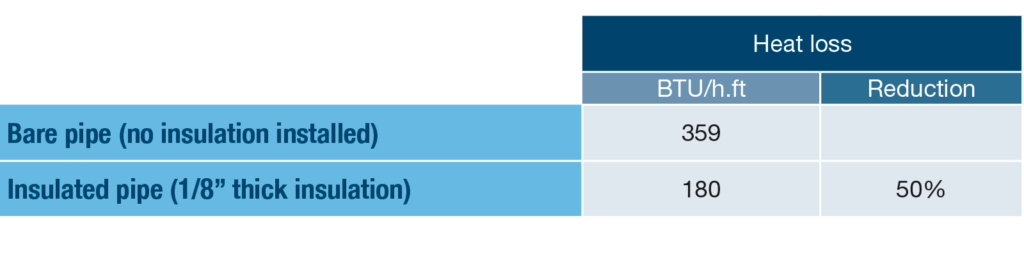
Increase the insulation thickness to ¼” and these are the results:
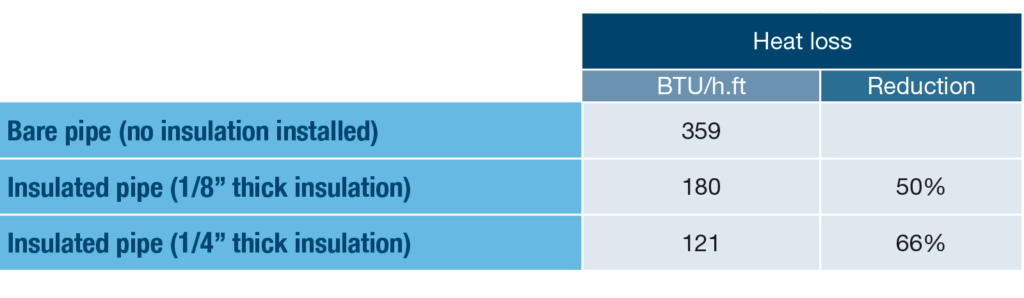
Now increase the insulation thickness to ½”:
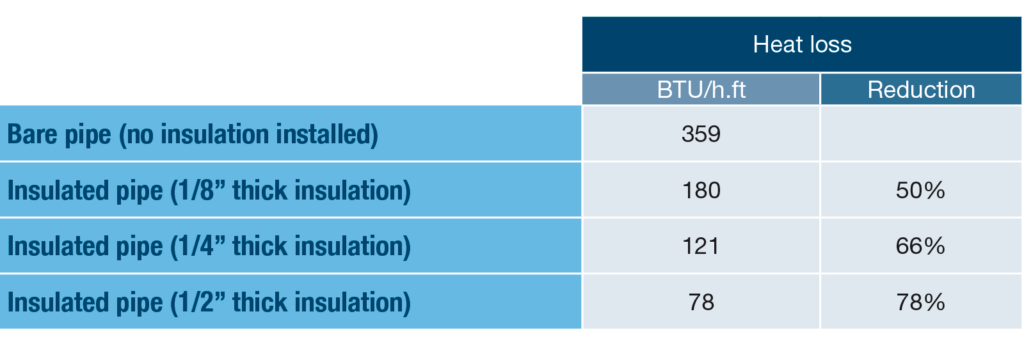
More bang for your insulation buck
What this shows is that just ½” of insulation, with an R-value of 2.03, reduces heat loss by 78 %. Apply it to our example — the 2”NB pipe running at 302°F — and compare its performance with insulation with other R-values and the results are eye-opening:
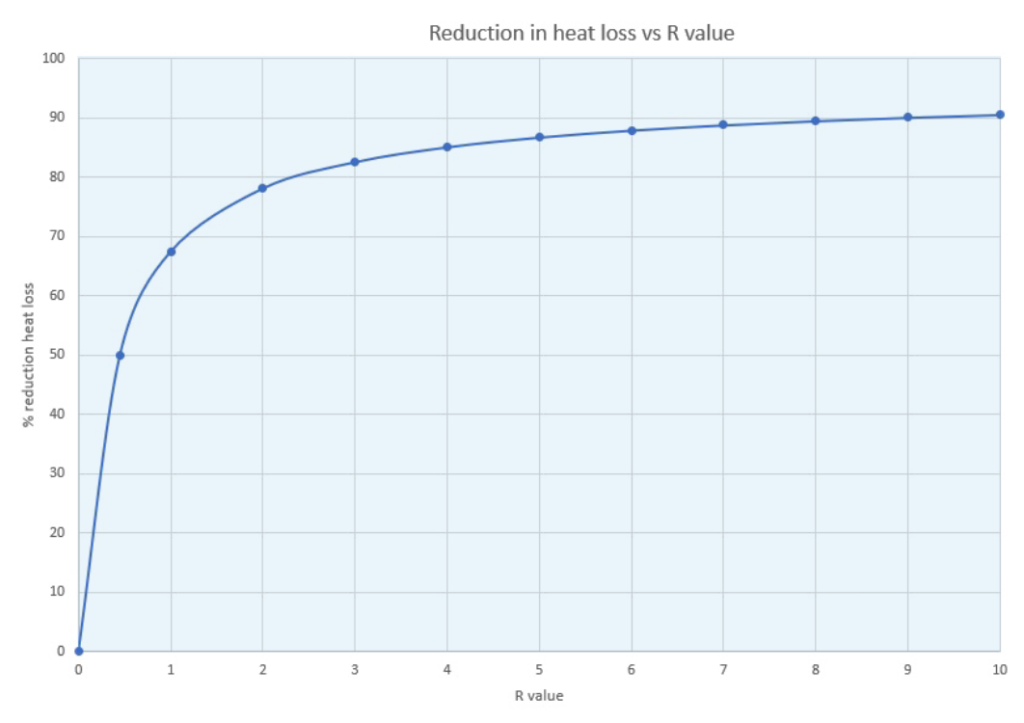
Open up to closed-cell insulation
Regarding R-values as the ‘be-all and end-all’ also ignores another key factor that contributes to insulation performance — whether the material chosen is of closed- or open-cell construction. This is important, because closed-cell products offer considerable benefits over open-cell products in several key areas:
Longevity and minimal maintenance: While reduction of heat loss in hot systems (heat gain in cold) is of primary importance, longevity of the insulation material is equally important — perhaps more — and can have a large influence over service lifetime. Closed-cell insulation requires minimal maintenance, providing further significant cost-savings over an extended service-life.
Moisture resistance: Moisture absorption of just 4% can degrade insulation performance by up to 70%. Open-cell materials naturally absorb moisture and rely on an outer cladding to prevent such ingress. In practice, ensuring continuity of such vapour barriers both during installation and over the lifetime of the insulation is difficult, and breakdown of the materials and corrosion under insulation (CUI) is common. By their very nature, closed-cell materials, on the other hand, do not absorb moisture or need an outer vapour barrier, and so do not contribute to CUI.
Wall thickness: Closed-cell products are supplied and readily available from ¼” thick, and so can insulate pipework in tight spaces — something difficult, even impossible, to insulate with thicker insulation — and the overall space allocated for pipe racks can be designed on smaller footprints.
Atmospheric contamination: Finally, closed-cell materials generally do not disintegrate or release any particles or pollutants into the work environment. In contrast, traditional thicker insulation products may release fibres and other pollutants to the atmosphere.
In summary, it pays in many ways to remember what the insulation is actually there for — reducing heat loss or gain. Ignore the received wisdom, cast off the ‘R-value blinkers’ and take a more holistic view of insulation performance.
1All evaluations referred to has been based on ISO 12241:2008, an industry-recognised calculation that which sets out rules for the calculation of heat-transfer-related properties of building equipment and industrial installations, predominantly under steady-state conditions.
Fungal contamination, most commonly by moulds and yeasts, is bad news for cleanroom manufacturing of pharmaceuticals. An outbreak can result in everything from product recalls, with the associated reputational brand damage, and production downtime through to actual harm to patients’ health.
From a production point of view, the relatively common fungus Aspergillus niger is known to contaminate raw materials stored in coldrooms prior to cleanroom manufacture. As for impacting patients’ health, contamination can reduce the therapeutic effectiveness of medicines. Creams and ointments are a prime example of products whose efficacy can be compromised because many fungi live off keratin, a protein found in skin, nails and hair.
A sobering example of the havoc that contamination can wreak when things really go wrong is the 2012 outbreak of fungal meningitis in the USA that killed over 100 patients and affected a further 798 after they received contaminated steroid injections manufactured by the New England Compounding Center (NECC) in Massachusetts. By December 2012, 400 lawsuits had been brought against the company as it filed for bankruptcy. Federal prosecutors charged 14 former NECC employees, including its president, with a host of criminal offences including sending out drugs that were unsanitary or contaminated.
Easy entry for fungi
Controlling contamination is made more challenging by the physical characteristics of fungal spores, which range in size from 1-50µ, and the ease with which they can enter environments by a wide variety of routes. Airborne spores can enter through windows, or via ducting and pipework – openings that also allow the ingress of moisture, in liquid or vapour form. This raises the relative humidity (RH) of the air, and a high RH is a big factor in contamination, as we shall see.
There are other routes for contamination to enter. As already noted, raw materials can be contaminated before entering the cleanroom, and the human factor shouldn’t be discounted, because employees can also bring contamination into the cleanroom. There is more than one example of a case of athlete’s foot causing an outbreak.
Once established in the cleanroom environment, fungal spores spread relatively easily and aggressively, and eradicating them can be difficult. There’s a wealth of advice available on how to remove mould — but prevention is infinitely better than cure. In practice, this involves specifying materials and components that will resist the development of mould, fungi and other microbial species, while providing the chemical stability, durability, purity and fire resistance that are essential features of materials used in cleanroom construction.
Critically important
The right choice of insulation is especially important. Condensation is a common cause of contamination, with cold pipework a significant concern wherever the temperature at the pipe’s surface falls below the dew point of its environment. As the air cools, the water vapour concentrated in the air starts to condense, and at the dew point for a particular temperature it becomes saturated in the air and condenses on surfaces as droplets — a perfect breeding ground for fungi.
A variety of cleanroom insulation products are available, under different brand names and manufactured from different materials. The principal solutions commonly found in cleanrooms include:
- open cell melamine foam
- EPDM elastomers
- closed cell PVDF polymer foam.
So how should cleanroom designers go about choosing the best insulation? It’s a given that the chosen product should conform to recognised performance standards, which in this case are set out in ASTM G21-15 (2025) Standard Practice for Determining Resistance of Synthetic Polymeric Materials to Fungi. This involves inoculating samples of the material under test with suitable organisms, then exposing them to conditions favourable to fungal growth. At set intervals, the samples are examined and rated for visual signs of growth.
Valuable as the ASTM G21-15 certification is in the selection process, however, it doesn’t reveal how the respective solutions perform compared to each other under the same test conditions. Such comparisons are especially important where project budget limitations might encourage decisions on price alone. Wherever possible, investment choices should be based on the most complete knowledge, considering factors such as the impact of catastrophic failure due to contamination, and ongoing service and maintenance costs. Increasingly, sustainability is a further key consideration.
It is possible to discover test results for individual brands in the public domain, for example, one manufacturer of open cell melamine insulation has published test results showing that fungal growth is evident after 21 days on its open cell melamine-based product — but genuine like-for-like comparisons have proved elusive until now.
‘Putting the best to the test’
Which is why, for the first time in the cleanroom insulation industry, Zotefoams plc, the foam specialists behind T-FIT® technical insulation, has commissioned independent performance testing that pitted T-FIT Clean against the leading EPDM elastomeric foam insulation brand to provide a suite of verified results.
The T-FIT story began over a decade ago, with customers in the pharmaceutical and biotech industries looking for a high-performance insulation solution for pipework in cleanrooms. T-FIT Clean, the resulting debut product line produced from Zotefoams’ ZOTEK® F42 HTLS high-performance PVDF foam, quickly earned recognition and countless installations in these industries and in semiconductor cleanrooms are testament to T-FIT Clean’s performance and longevity.
Nottingham, UK-based Murphy & Son was appointed to carry out the testing based on its 130-plus year history of supporting the brewing industry, where the fermentation process presents a recognised risk area for fungal contamination and its consequences are well understood.
During testing, samples of T-FIT Clean and the EPDM product were pre-cleaned with 70/30 ethanol water to remove any surface contamination which might potentially sustain mould growth. In temperatures of 28-30oC and a relative humidity of ≥85% they were then exposed for 28 days to a variety of fungi (see Table 1), including the two most commonly found in a cleanroom environment — Aspergillus and Aureobasidium.
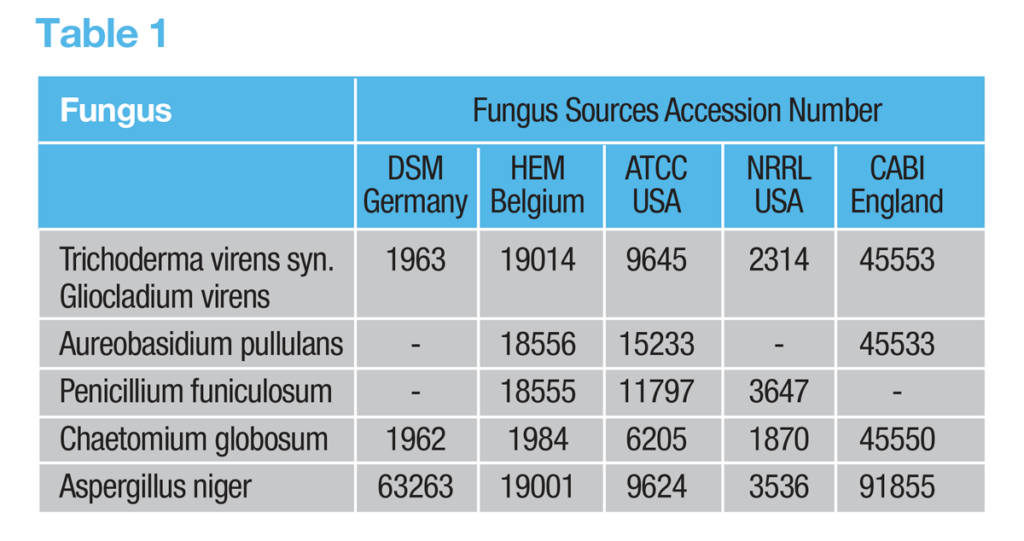
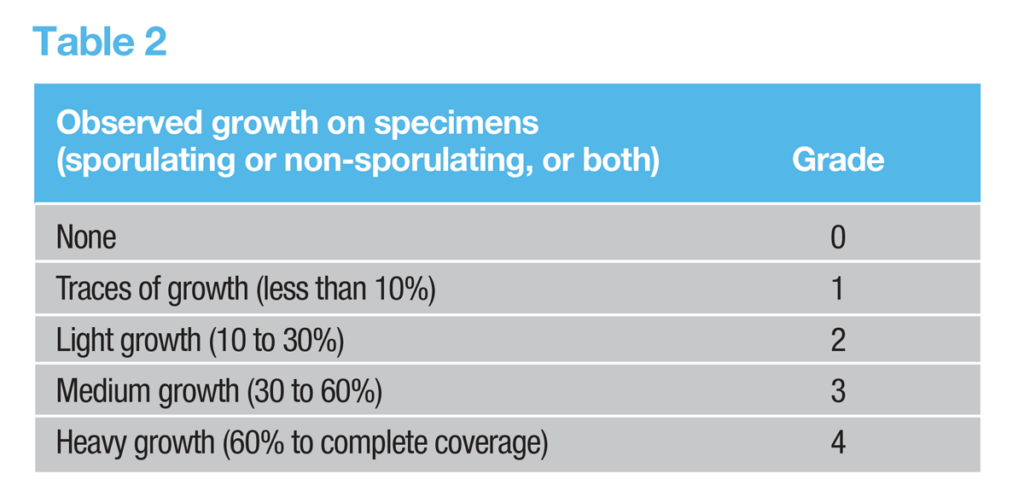
The verdict
The T-FIT® Clean sample tested received a mould growth rating of 0, with no sign of growth observed, as these post-test photos and close-up images of the sample show:
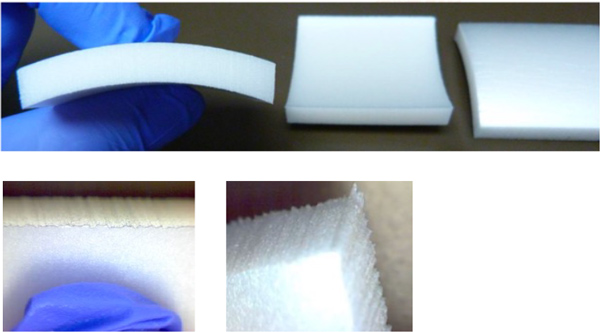
By contrast, the EPDM elastomeric foam product was rated 2 and — as is clear from the images below — displayed clear visual evidence of mould growth:
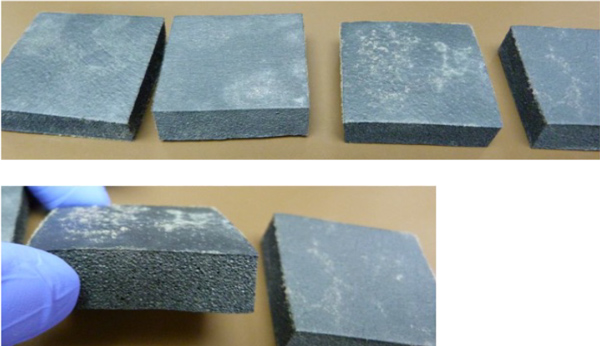
Clearly superior
Thanks to these tests, the market now has concrete evidence of T-FIT’s class-leading resistance to fungal contamination, clearly demonstrated by the 0 rating versus the marketing leading EPDM elastomeric foam’s rating of 2. This exceptional performance is a result of the high purity ‘inert’ surface characteristic of T-FIT products, which does not readily support the growth of microorganisms.
Key to the performance characteristics of T-FIT products is Zotefoams’ unique three stage manufacturing process, which uses pure nitrogen as a foaming agent to create materials of exceptional calibre compared to products expanded using chemical foaming agents. In Stage 1, pure PVDF polymer is extruded into a solid slab, then irradiated to create chemical bonds that join the polymer chains (crosslinking). Resulting material properties include excellent thermal stability, high strength and toughness compared to non-crosslinked materials; crosslinking via irradiation also prevents the shrinkage that is often associated with thermoplastic materials. Stage 2 applies extremely high pressures and temperatures to dissolve the nitrogen gas into the slabs. In Stage 3 the nitrogen-saturated slabs are put through a second, high temperature, lower-pressure cycle where the pressure is gradually released to allow the free expansion of the material into sheets of foam.
The result is a fine, completely closed cell structure that is fibre-, dust- and particulate-free, and highly resistant to bacteria and mould growth. T-FIT Clean’s ASTM G21-tested performance on zero fungal growth brings long-term protection against the risk of product contamination. Compared to open cell materials, T-FIT more effectively limits moisture and gas penetration because there is no continuous network through which substances can travel.
For high-temperature environments, T-FIT Clean offers exemplary fire safety credentials. Rated 5/45 (Flame-Spread Index/Smoke Development Index) according to ASTM E84 for surface burning characteristics of materials, T-FIT Clean delivers the lowest flame, smoke and toxicity rating of any polyester/elastomer insulation.
A wide temperature operating range — from -80oC to +160oC — combined with the durability of the material ensures thermal performance remains unimpaired in the long term, even where repeated cycling between chilled process temperatures and high cleaning temperatures (clean in place, sterilise in place) is involved.
Test the best with a free trial installation
T-FIT offers customers the opportunity to ‘put the best to the test’ for themselves under ‘real-world’ cleanroom conditions with a free trial installation of T-FIT Clean. To request a trial, or for further information about the comparative testing, contact us at
t-fitsales@zotefoams.com
In 2019 the estimated value of the global market for cleanroom technology was $3.7 billion, with an expected compound annual growth rate (CAGR) of 4.6% that would take it to $5.3 billion by 2027.
The pharmaceutical sector accounts for almost half the value and is a significant driver of the growth. As products become ever more sophisticated, and regulatory controls correspondingly stricter, the construction and operation of safe, sterile cleanroom environments is critically important.
The materials employed must combine chemical stability, durability, purity, and fire resistance; they must shed no particulates and emit no VOCs; they must prevent the development of mould, fungi and other microbial species; and they must be robust enough to withstand aggressive chemical and high-temperature cleaning. Poor performance in any of these areas can have catastrophic consequences, from costly production downtime to the contamination — and consequent destruction — of entire production batches.
Because the pharmaceutical cold chain effectively starts in the cleanroom, choosing the right insulation is a crucial first step in maintaining quality. As is clear from the checklist of features just described, the cleanroom environment is a challenging one for insulation, and the challenges are especially apparent in the pipework and ducting that provide the essential underpinning of the cleanroom’s functions.
An effective pipework insulation solution must perform a number of functions, starting with preventing condensation, a common cause of contamination. Condensation will form on chilled process pipework if the temperature at the pipe’s surface falls below the dew point of its environment. Uncontrolled, condensation can lead to corrosion of the pipework. To prevent this happening, it is necessary to raise the surface temperature of the pipework above the dew point, so that droplets do not form on the surface of the insulation.
At the same time, the chosen solution must deliver peak performance on pipes that are subject to wide temperature variation — chilled one moment, then subject to high-temperature steam cleaning the next. A wide operating temperature range is therefore essential.
A further factor to consider is space — or rather the lack of it — because space is usually at a premium around cleanroom pipework. Choosing insulation with a slim profile and compact footprint is therefore critical, to successfully negotiate complex, congested pipe runs. It needs to also be aesthetically pleasing to maintain the clean connotations that a cleanroom typifies. And then there are questions such as ongoing maintenance, which needs to be as straightforward as possible, and the service life: you don’t want to be interrupting production every few months to replace worn out insulation.
Chinese biological products developer and manufacturer Shenzhen Kangtai faced all these issues when the company expanded and upgraded the cleanroom manufacturing facilities at its Shenzhen headquarters. A review of the cleanroom environment was part of a companywide programme of investment in production processes and identified several areas where insulation could be improved. These included replacing the existing rubber insulation, which was too thick and bulky to be used in parts of the pipework where space was tight. In addition, maintaining the necessary stringent levels of cleanliness took more time and effort.
Further challenges were posed by a testing combination of high- and low-temperature pipe runs. Steam lines operating at 130-160oC not only consumed excessive energy but raised safety issues for cleanroom staff, while low-temperature chilled water lines (2-5oC) caused condensation and energy loss.
The Shenzhen Kangtai project team considered several possible solutions before deciding on the T-FIT® Clean insulation product range. T-FIT® Clean is manufactured exclusively from ZOTEK® F42HTLS closed-cell Kynar® PVDF foam and offers a number of features that matched Shenzhen Kangtai’s requirements. These include an operating temperature range of 0oC~150°C, low VOC and thanks to the closed-cell structure helps prevent corrosion under insulation (CUI) while offering a smooth surface that is easy to clean. In addition, with a thickness of just 6.35mm, T-FIT® Clean fits into the smallest spaces to effectively insulate even the most complex pipe runs.
Shenzhen Kangtai also appreciated the ease with which T-FIT® Clean can be installed, with a minimum of fuss, tooling, or disruption to any cleanroom operation. Because it is guaranteed to be particulate-free, installation can take place during production, without the need for PPE or special containment requirements such as tents or hoods. In the case of Shenzhen Kangtai, the installation involved hardly any interruption to production. In total, installation took under one month, and for 80% of that time production continued uninterrupted.
Three-stage process
These characteristics are the direct result of the unique three-stage manufacturing process developed by Zotefoams, which uses pure nitrogen as a foaming agent to create a premium foam with significant advantages over products expanded using chemical foaming agents.
In Stage 1 pure PVDF polymer is extruded into a solid slab, then physically crosslinked using irradiation. As a result, the polymer chains that make up the material are joined by chemical bonds, and these linkages give the material thermal stability, high strength and toughness compared to non-crosslinked materials. Stage 2 applies extremely high pressures and temperatures to dissolve the nitrogen gas into the solid slabs. In Stage 3 the nitrogen-saturated slabs are put through a second, lower-temperature cycle where the pressure is released to allow the free expansion of the material into sheets of foam.
The result is a fine, completely closed-cell structure that is fibre-, dust- and particulate-free, and highly resistant to bacteria and mould growth. T-FIT Clean’s ASTM G21-tested performance on zero fungal growth brings long-term protection against the risk of product contamination. Inherently hydrophobic, the technology also prevents condensation and moisture. For high-temperature environments, T-FIT® Clean offers exemplary fire safety credentials. Rated 5/45 per T-FIT Clean according to ASTM E84 for surface burning characteristics of materials, T-FIT Clean delivers the lowest flame, smoke and toxicity rating of any polyester/elastomer insulation.
A wide operating range — from -80oC to +160oC — enables T-FIT insulation to perform at both chilled process temperatures and high cleaning temperatures without any loss of thermal performance, and so can be used on pipework subject to ‘clean in-place’ processes. Compared to open-cell materials, T-FIT more effectively reduces moisture and gas penetration through the material because there is no continuous gas network through which substances can be transferred.
Fast, easy installation
T-FIT’s flexible, slimline tubes are easily adapted to the demands of complex, congested pipe runs featuring unusual bends or hard-to-reach areas. The tubes are complemented by matching tees and bends, installation is quick and simple, and so it’s easy to integrate, reducing labour costs, downtime and the Total Cost of Ownership. Because the advanced cellular materials are intrinsically pure, odour-free, and non-toxic, no harmful chemicals, fibres or dust are given off during installation or the lifespan of the product.